HOW DOES A PHASE CONVERTER WORK?
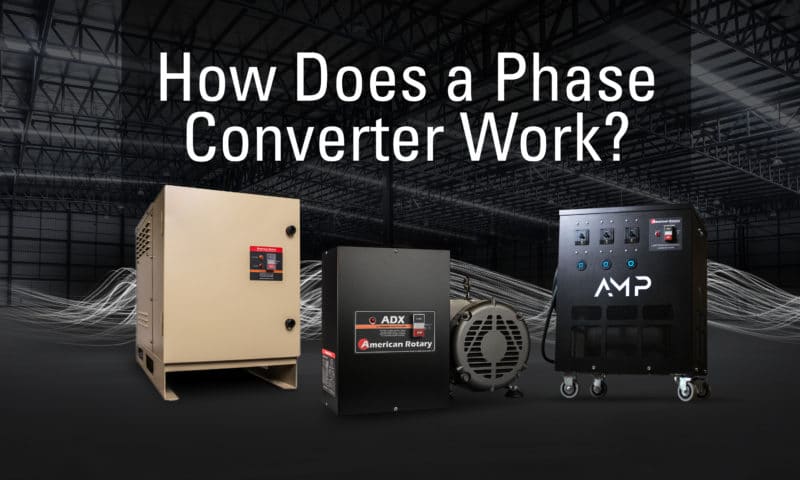
A phase converter uses a motor to convert single-phase electricity—the typical utility electric power service—into the three-phase power required by many different types of heavy-duty industrial equipment. It’s a great tool where three-phase power is either unavailable or too costly to install.
If you have a shop that uses powerful machinery—for woodworking, metalworking, CNC machining, foodservice, farming and more—you need three-phase power. Trouble is, getting three-phase power can be hard to come by in some places. In others, it’s simply too expensive to install.
A phase converter may be your best bet to get your three-phase equipment up and running just like it would run if you had utility three-phase power. But, what exactly is a phase converter? How does it work? What are the types of phase converters available?
This article will outline the basics of what you need to know about phase converters to help ensure you can find your best solution.
WHAT IS A 3 PHASE CONVERTER?
A 3 phase converter is a device used to help power a wide variety of machines and industrial equipment that requires three-phase electricity, in places where this service is not available from the utility or is too costly to install because you’re in a remote location.
Electric utilities supply power of two main types: single-phase and three-phase systems. The main difference is that a single-phase circuit has one conducting and one neutral wire, while three-phase power has three conductor wires and one neutral wire. You can find more detail about the difference between single phase and three phase power here.
Single-phase power is the common residential and light-commercial variety, used in places with smaller electricity loads requiring less power. Three-phase utility service is used in large industries, factories, and in manufacturing units where a large amount of power is required.
Example use cases include:
- Agriculture: Farms use lots of heavy-duty equipment but are often in areas without access to the 3-phase power grid.
- Food service: Pizza ovens, regular ovens, rotisseries and ice cream machines are among many voltage-sensitive three-phase-powered systems.
- Woodworking: Shops often need to start and run multiple 3-phase machines with varying load conditions (sometimes simultaneously).
- Machining: CNC milling machines, lathes, PLCs, EDMs and other equipment relies on precisely balanced three-phase power.
- Metalworking: Applications include wire EDMs, CNC lathes, CNC mills and other voltage-sensitive equipment, as well as lighter loads.
- Other industrial: If you have any equipment that performs tough jobs, chances are it takes three-phase power.
Three-phase power from the utility company is not always available for all these different needs. And even if it is, it can be cost-prohibitive. A utility will generally charge a higher fee for three-phase service because of the extra equipment, including transformers, metering, and distribution wire.
On average, the cost to bring in three-phase utility power is approximately $50,000 per mile (even as high as $90,000, according to ScienceStruck) plus site prep costs.
The cost on average for usage is about $0.10 per kilowatt-hour (kWh) plus minimum usage requirements and demand charges. With utility three-phase power, your power quality is roughly at a 10% voltage balance across the three legs.
If the three-phase utility is a route you choose, it’s a good idea to do a true cost analysis to know all of your costs upfront before investing in having it brought in.
The three-phase converter gets around this issue by converting single-phase electricity into three-phase for you.
WHAT DOES A PHASE CONVERTER DO?
A phase converter creates an additional line or phase of voltage by adding an induction motor or idler/generator to the system.
The two main types are static phase converters, which can start a three-phase load but only run it under lower single phase power; and rotary phase converters, which use a control panel with a start circuit to create true and well-balanced three-phase power.
WHAT IS A STATIC PHASE CONVERTER?
The straightforward static phase converter will start a 3-phase load but run it only under single-phase power, limiting the load to about 2/3 of its rated capacity.
Capacitors help start the three-phase motor, but then are disconnected once the motor is up to speed. At that point, the system is effectively only running lower single-phase power. A static phase converter, therefore, is not usually suitable for heavy-duty three-phase equipment.
WHAT IS A ROTARY PHASE CONVERTER?
A rotary phase converter is a more sophisticated unit that creates true three-phase power, often more precise than utility-supplied three-phase power.
A rotary phase converter is a cost-effective option to provide three-phase utility to your shop. This choice gives you the option to run three-phase equipment off single-phase power whether it’s from the utility company, a generator, or a solar power system.
With many different sizes available, you can tailor your needs to operate one single load at one time, all the way up to a whole three-phase operation. That flexibility can also make the rotary phase converter option very affordable compared to the other three-phase options.
HOW DOES A ROTARY PHASE CONVERTER WORK?
A rotary phase converter uses a control panel with a start circuit and run circuit to create balanced, clean power without excessive voltage. A three-phase idler/generator motor produces the third leg of power.
Some rotary phase converters are digitally controlled, enabling them to produce balanced power that is clean enough to run on voltage-sensitive loads such as a CNC machine, welder, or any other computer-controlled load.
A rotary phase converter does not change the voltage, but it can be paired with a transformer to step the voltage up or down depending on what’s needed.
To give you a better sense of your options, here’s an overview of rotary phase converters available from American Rotary:
- AR General Purpose: Designed for light- to medium-duty, general-purpose loads such as mills, single speed lathes and drill presses.
- AD Digital Smart Series: For CNC, VFD, rectified and any other voltage sensitive equipment.
- ADX Extreme Duty Series: Current control to provide consistent torque while starting high inertia, extremely hard-starting loads such as pumps, fans, compressors, blowers, dust collectors and flywheels.
- AUL UL Listed: Providing all the power and features of our ADX line, but with UL licensing to meet state or local requirements.
- AI Industrial Grade: With a Type 3R enclosure for ultimate protection in demanding industrial and agricultural applications.
- AMP Mobile: Plug-and-play ready for a quick, cost-effective installation.
HOW EFFICIENT IS A PHASE CONVERTER?
We hear many questions and misconceptions about the efficiency and quality of the power supplied by phase converters.
For example, you might have heard that phase converters draw a huge inrush current upon start-up. This disproportionate power draw can end up bothering neighbors by dimming their lights. It can also lead to demand charges and large increases on power bills.
These issues highlight why it’s important to look for a phase converter that has variable impedance technology built directly into the idler/generator. This design drastically reduces inrush (starting) current, resulting in reliable starts, every time, with no voltage drop. Read more about the advantages of this rotary phase converter setup.
Unfortunately, many phase converter manufacturers claim that they have such technology, when they instead use a regular stock motor, rewire it for low voltage, and cut off the exposed rotating shaft, which is also a huge safety hazard. This article can help you identify which type of idler motor a phase converter uses.
HOW EFFICIENT IS A ROTARY PHASE CONVERTER?
A rotary phase converter, particularly one that incorporates digital control, can be an efficient way to provide three-phase utility to your shop.
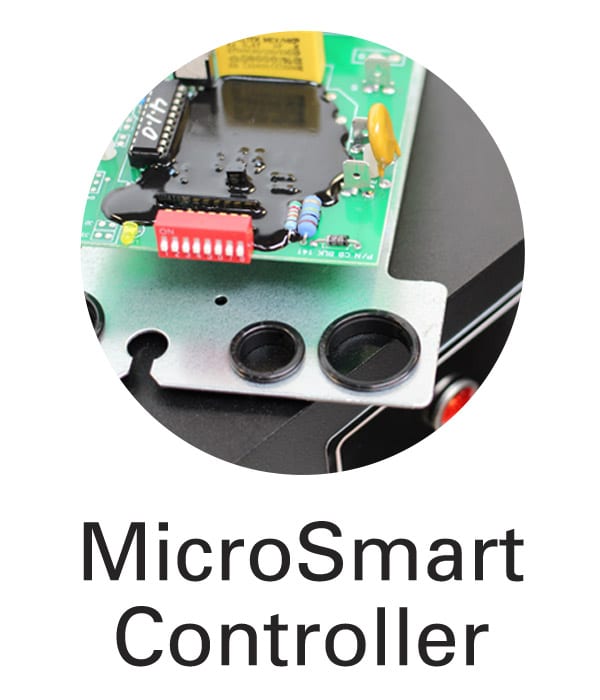
For example, American Rotary’s digital rotary phase converter lines (AD, ADX, and AI) feature the patented MicroSmart Controller. This digital controller monitors and controls your voltages across the three phases/legs of power, providing precise voltage balance to your equipment and adding additional fail-safe features to your phase converter operation.
With MicroSmart Controller, you can expect to see voltages around a 2-5% balance across the three legs.
This voltage balance is important, especially because voltage variations over 5% can damage some equipment, especially CNC machines. Therefore, even a small imbalance can necessitate a large reduction in motor power to protect the equipment.
By monitoring your voltage every 50 milliseconds and providing better voltage control, this helps prolong the life of your converter, allows significantly more load capacity (ADX and AI), and will run your equipment more efficiently.
With all American Rotary phase converters, they use a custom-designed induction generator as their idler. The VIT Generator is a true soft start idler that uses 1/3 of the inrush current of a comparable three-phase motor.
This virtually eliminates demand charges from the utility and that dreaded dimming of the neighbor’s lights—allowing you to run the phase converter 24/7 at little to no load without any negative effects. These idlers run very smoothly, quietly and efficiently.
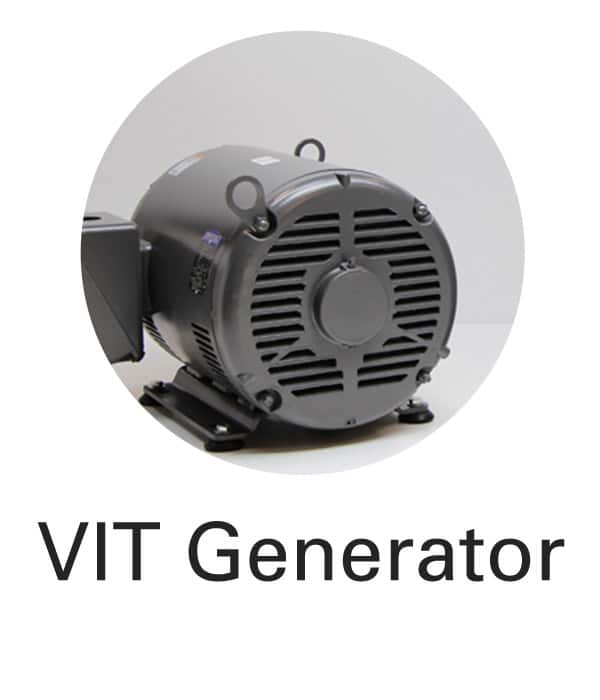
Lastly, this technology produces a true three-phase sine wave, allowing you to run your equipment on full three-phase power off a single-phase power source. You will have a voltage balance of about 5% or greater when measured leg to leg, which makes it suitable for CNC and other voltage sensitive applications. The approximate cost of running a rotary phase converter is $0.12 per kWh.
Compare that to the $50,000 installation of three-phase utility power, with average usage cost of about $0.10 per kWh, plus minimum usage requirements and demand charges. With utility three-phase power, your power quality is roughly at a 10% voltage balance across the three legs.
Clearly, if the three-phase utility is a route you choose, it’s a good idea to do a true cost analysis to know all of your costs upfront before investing in having it brought in.
CHOOSING THE RIGHT ROTARY 3 PHASE CONVERTER
Having a rotary three phase converter saves you from having to worry about the large expense of bringing in three-phase utility power, having minimum usage requirements, or worrying about having a loud, fuel-guzzling generator on site to power your shop equipment.
Sound like the right solution for your needs? Great! Then it’s time to start choosing your converter.
You’ll first need to verify that you have enough single-phase power available for your setup. Then consider what type of load you’re running: Is it light, medium, heavy duty? Horsepower specifications are also key. So is where you’ll be putting the converter—inside or outside?
Give us a call today!